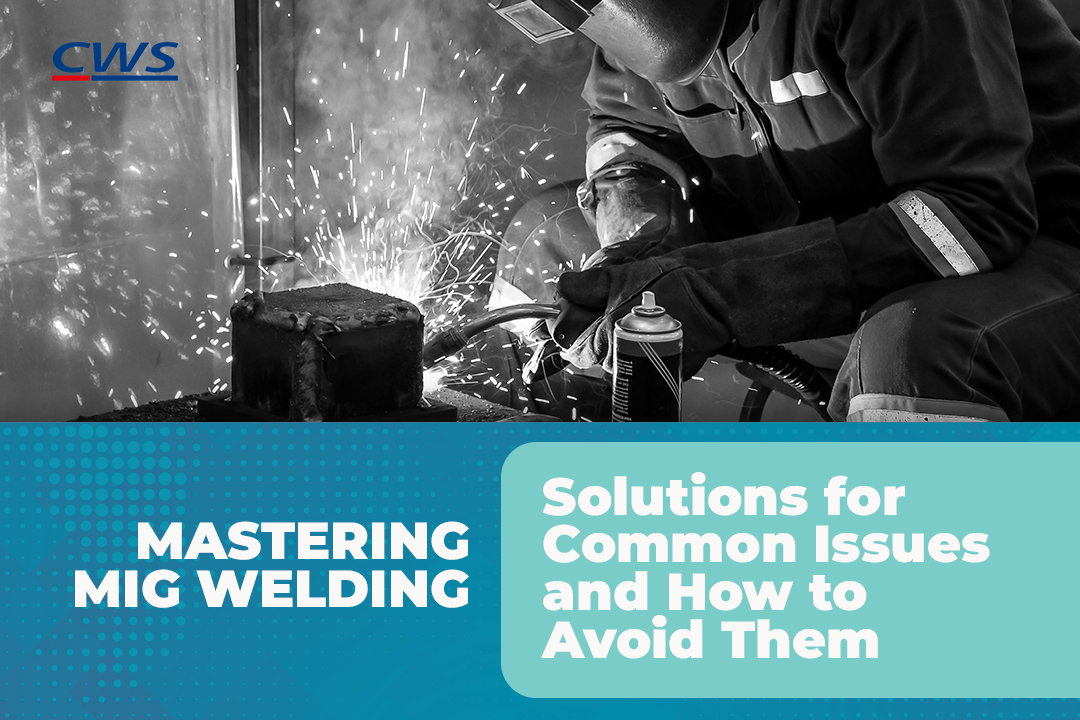
Mastering MIG Welding: Solutions for Common Issues and How to Avoid Them
MIG welding, also known as Gas Metal Arc Welding (GMAW), is one of the most popular welding methods in the industry due to its speed and ease of use. However, even experienced welders encounter problems during MIG welding. Poor penetration, uneven bead appearance, wire feeding problems are some of the common issues that may arise during MIG welding. In this blog, we'll discuss these issues and provide tips on how to troubleshoot them to ensure you achieve high-quality welds.
Poor Penetration
Poor penetration is a common problem during MIG welding and can result in weak and unreliable welds. This issue is usually caused by insufficient heat input, which leads to incomplete fusion between the base metals. To troubleshoot poor penetration, consider the following:
- Increase the amperage: Increasing the amperage will increase the heat input, which can help to achieve better penetration.
- Adjust the travel speed: Increasing the travel speed can also help to increase the heat input and improve penetration. However, be careful not to increase the speed too much, as this can result in poor bead appearance and insufficient fusion.
- Check the electrode extension: The electrode extension, or stick-out, is the length of wire that extends from the contact tip. If the electrode extension is too short, it can cause poor penetration. Check the manufacturer's recommendations for the correct electrode extension.
- Check the gas flow: Insufficient gas flow can result in poor penetration. Ensure that the gas flow rate is set correctly and that there are no leaks in the gas supply.
Uneven Bead Appearance
Uneven bead appearance is another common issue that may arise during MIG welding. This can result in an inconsistent weld with poor aesthetics. To troubleshoot uneven bead appearance, consider the following:
- Adjust the voltage: Increasing the voltage can help to produce a wider and flatter bead. Decreasing the voltage can help to produce a narrower and taller bead. Experiment with different voltage settings to achieve the desired bead appearance.
- Adjust the wire feed speed: Increasing the wire feed speed can result in a wider and flatter bead. Decreasing the wire feed speed can result in a narrower and taller bead.
- Check the contact tip size: The contact tip size should match the diameter of the wire being used. Using a contact tip that is too small can result in a narrow and tall bead, while using a contact tip that is too large can result in a wide and flat bead.
- Check the wire type: Different types of wire may produce different bead appearances. Experiment with different wire types to achieve the desired bead appearance.
Wire Feeding Problems
Wire feeding problems are another common issue that may arise during MIG welding. This can result in an inconsistent wire feed, which can affect the quality of the weld. To troubleshoot wire feeding problems, consider the following:
- Check the wire feed speed: The wire feed speed should be set correctly for the wire diameter being used. If the wire feed speed is too high, it can cause the wire to birdnest or tangle. If the wire feed speed is too low, it can cause the wire to burn back.
- Check the wire tension: The wire tension should be set correctly to ensure consistent wire feed. If the tension is too loose, the wire may slip or birdnest. If the tension is too tight, it can cause the wire to deform or kink.
- Check the wire quality: Poor quality wire can cause feeding problems. Ensure that the wire is clean and free from rust or other contaminants. Using a high-quality wire can help to improve wire feed consistency.
- Check the wire liner: The wire liner should be clean and free from kinks or deformations.
Burn-Through
Burn-through is a common issue that may occur during MIG welding. It happens when the welding heat is too high and melts through the base metal, leaving a hole. To troubleshoot burn-through, consider the following:
- Reduce the amperage or voltage: Reducing the amperage or voltage can help to lower the heat input and prevent burn-through. Be careful not to reduce the settings too much, as this can result in poor penetration and weak welds.
- Adjust the travel speed: Increasing the travel speed can help to reduce the heat input and prevent burn-through. However, be careful not to increase the speed too much, as this can result in poor fusion and weak welds.
- Use a thicker base metal: Using a thicker base metal can help to prevent burn-through. Thicker metals can absorb more heat, allowing for a higher amperage or voltage to be used without causing burn-through.
Porosity
Porosity is another common issue that may occur during MIG welding. It happens when small gas pockets form in the weld, which can weaken the structure and lead to failure. To troubleshoot porosity, consider the following:
- Check the gas flow rate: Insufficient gas flow can cause porosity. Ensure that the gas flow rate is set correctly and that there are no leaks in the gas supply.
- Check the welding position: Welding in an awkward position or at an angle can cause porosity. Ensure that the welding position is comfortable and allows for proper gas coverage.
- Check the wire quality: Poor quality wire can cause porosity. Ensure that the wire is clean and free from rust or other contaminants. Using a high-quality wire can help to reduce porosity.
Spatter
Spatter is another common issue that may occur during MIG welding. It happens when small droplets of molten metal spray out of the weld, which can create a mess and affect the aesthetics of the weld. To troubleshoot spatter, consider the following:
Adjust the voltage: High voltage can cause spatter. Decreasing the voltage can help to reduce spatter. However, be careful not to decrease the voltage too much, as this can result in poor fusion and weak welds.
Adjust the wire feed speed: High wire feed speed can cause spatter. Decreasing the wire feed speed can help to reduce spatter. However, be careful not to decrease the speed too much, as this can result in poor fusion and weak welds.
Use an anti-spatter spray: Using an anti-spatter spray can help to prevent spatter. Apply the spray to the welding gun nozzle and surrounding areas before welding. This will help to prevent spatter from sticking to the surfaces and make cleanup easier.
By understanding these common MIG welding problems and their solutions, you'll be better equipped to troubleshoot issues that may arise during welding. With a little practice and experimentation, you'll be able to achieve high-quality welds that meet your project's requirements.